News
Two American Bridge Projects Receive OCEA Honor Awards
Two American Bridge Projects Receive OCEA Honor Awards https://www.americanbridge.net/wp-content/themes/corpus/images/empty/thumbnail.jpg 150 150 American Bridge American Bridge https://www.americanbridge.net/wp-content/themes/corpus/images/empty/thumbnail.jpg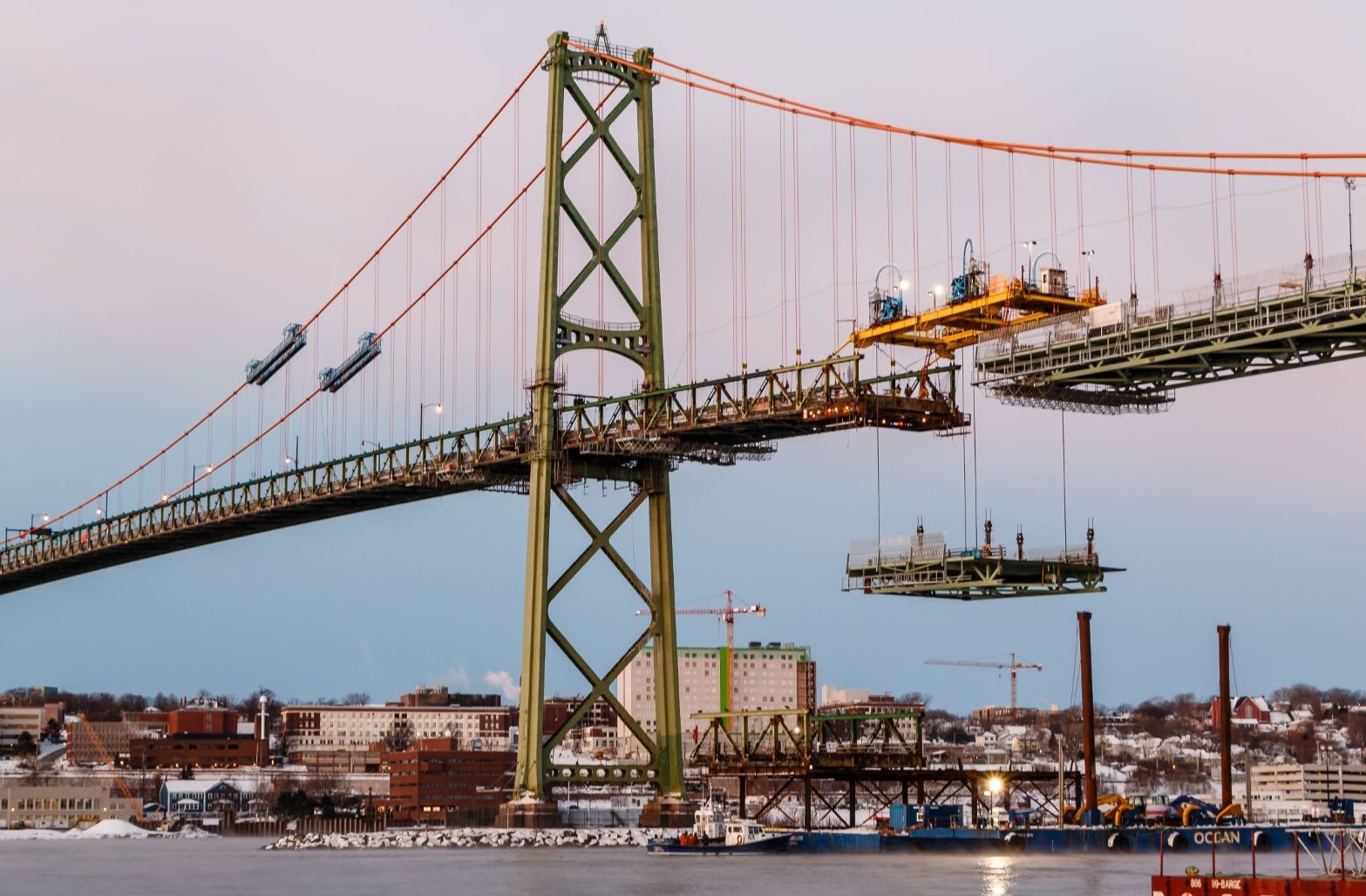
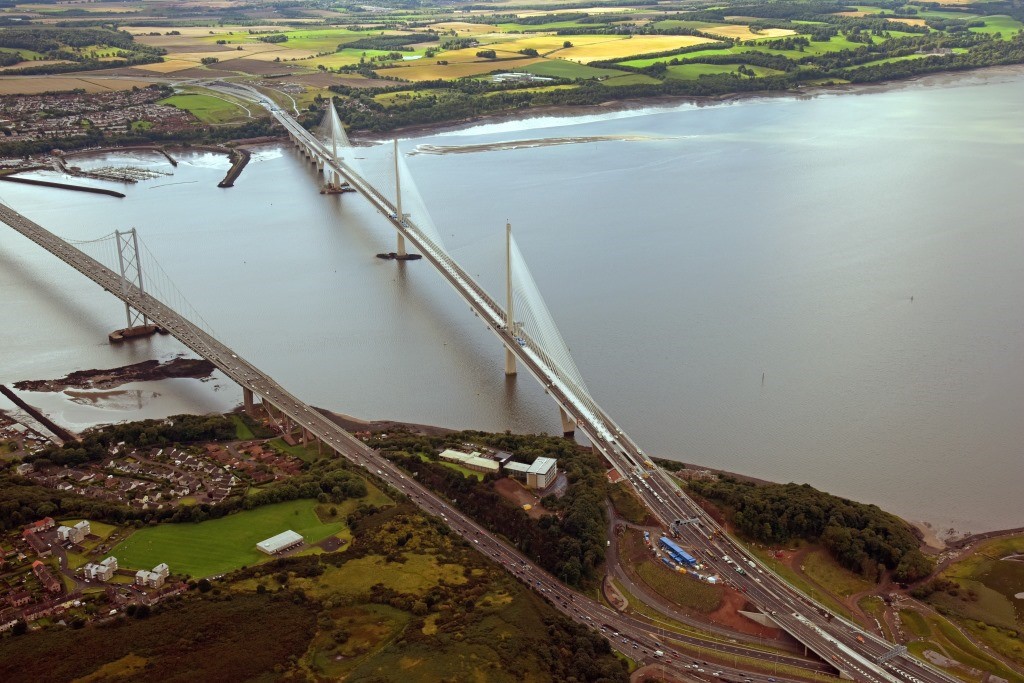
Washington, DC. The American Society of Civil Engineers (ASCE) named two American Bridge Company projects as Outstanding Civil Engineering Achievement (OCEA) Honor Award recipients. This award represents projects that illustrate superior engineering skills and represent a significant contribution to the progress of civil engineering. The AB projects include the Angus L. Macdonald Bridge Superstructure Replacement (also known as The Big Lift) in Halifax, Nova Scotia, Canada and the Queensferry Crossing in Edinburgh, Scotland. The projects were showcased, on March 13th, at the OPAL Gala in Washington, D.C. where it was announced that the Queensferry Crossing became this year’s OCEA Bronze winner. Congratulations to both AB teams on this outstanding achievement!
The Angus L. Macdonald Bridge is a 2,500-foot-long suspension bridge that spans the Halifax Harbour, connecting Dartmouth with downtown Halifax. As General Contractor on the bridge superstructure replacement, AB utilized innovative techniques to demolish and replace the entire stiffening truss and roadway system. The superstructure replacement work included removing existing 30 feet and 65 feet deck segments and replacing them with orthotropic deck truss segments. AB developed a comprehensive procedure for replacing each segment, with individual durations ranging from ten minutes to three hours. During weekend closures, the team was able to replace two segments at a time. The grid deck was soft cut in advance and the structural members were cut during the outage. Segments were then lowered down to a barge with strand jacks and the new segment was raised and installed.
In addition, AB also replaced 148 hanger assemblies totaling 102.5 tons installed new handstrands, replaced six cable bands, and 140 cable band waisted rods. In each of the three suspended spans, two existing cable bands were removed and replaced with larger cast and machined cable bands. While these cable bands were replaced, the existing traction rods, which restrain the spans longitudinally, were also replaced. The existing cable bands were clamped to the main cable with six, 1.6-inch diameter bolts, while the new cable bands used 28 to 48 1.25-inch diameter waisted rods. The additional clamping force between the new cable bands and the main cable was required to resist the longitudinal forces imparted by the new traction rods. Waisted rods in each new cable band were tensioned simultaneously with custom hydraulic bolt tensioners. Each rod was then measured with a custom extensometer to ensure the proper elongation and the proper load has been reached.
Other existing cable bands remained in place, but still required additional clamping force to prevent slipping under the higher hanger loads during construction. In these locations, the existing cable band bolts were replaced one at a time with waisted rods, which were tensioned with the hydraulic bolt tensioner and checked with the extensometer. The change in length of the existing cable band bolts was also measured to determine the original tension in the bolts. Based on these measurements, nearly 600 cable band bolts were replaced with waisted rods. The cable bands were accessed from the two, 155.75-foot long cable crawlers with a self-contained winching system, which allowed each crawler to move up and down the cable without the need for an external anchorage.
Following segment replacement, a threaded jacking assembly at each hanger was used to sequentially shorten each hanger and raise the bridge deck. This raising of the suspended spans provided an additional three meters of clearance to the water at the center of the Main Span, accommodating larger shipping vessels. To provide this additional clearance, each hanger was jacked in increments of no more than five inches, for over 656 feet of total jacking. Once complete, a cable dehumidification system for the main cables was installed as well as a stainless-steel wrap for cable hardening.
This was only the second time that the suspended spans of a suspension bridge was replaced while keeping the bridge open to traffic. The first was also completed by AB on the Lions Gate Bridge.
The second project award went to the record-breaking Queensferry Crossing, which was named the OCEA Bronze winner. The project corridor stretches almost 14 miles, and includes includes the world’s longest three tower cable-stayed bridge at 8,654 feet, and spans the Firth of Forth in Edinburgh, Scotland. The scope also included major motorway upgrades to the north and south of the bridge. The two main navigation spans are each 2,132.5 feet long. The bridge has 14 spans, three concrete towers in the center of the transverse cross section up to 689 feet tall, two planes of stay cables that anchor in the center of the structure and a composite steel tub/concrete deck superstructure. The cable stay bridge superstructure was erected mainly by deck mounted gantries. Overall, there are 13 main bridge foundations, including three excavated caissons, one precast cofferdam, five marine sheetpile cofferdams, one land sheetpile cofferdam and three conventional pile or spread footings.
Prior to the completion of the final closure sections on the deck, the balanced cantilevers were recognized as the longest ever by the Guinness Book of World Records. It is also the longest three-tower, cable-stayed bridge in the world at 1.7 miles and the biggest infrastructure project in Scotland in a generation. It has the highest bridge towers in the UK at 689 feet. A new world record was achieved in 2013 when the team performed the largest continuous underwater concrete pour, depositing 595,723 cubic feet of concrete into the water-filled south tower caisson non-stop in 24 hours.
This important link between Lothians and Fife was built to alleviate traffic from the Forth Road Bridge, and is projected to carry about 24 million vehicles per year with a life expectancy of 120 years.
Due to the size of the complex design-build, the team established an instrumental project management system from the project outset. Management teams, organized around project scope, worked collaboratively and coordinated closely with other teams. For example, the field engineering staff initially began their work assignments in the engineering department. As the works proceeded from design to construction phases, the engineers progressed to the work area teams, where they managed execution of now familiar work scopes. Growing out of the work planning phase where they were exposed to the total project, they retained appreciation for the overall goals of the project and knowledge of resources that might be shared in the execution.
Like all AB projects, quality and safety was incorporated into all phases of the project, including work planning. Work plans included a section for quality that contains inspection and test plans for QC and hold points for QA. The work planning process resulted in less time lost to miscommunication and provided a clear closeout and punch list procedure that aided in quickly resolving issues prior to opening the bridge to traffic. AB also implemented a comprehensive health, safety, and environmental management program which is based on rigorous company standards but includes customized plans that were specifically developed for the needs of the project. This project provided unique training opportunities as employees need to be trained in cold weather search and rescue procedures prior to being able to work over or near the Firth of Forth. Special personal protective suits were provided to protect against hypothermia and allow for response time and rescue.
Innovations included a wide variety of technical and commercial measures that enabled the team to be the low bidder for the project. This included the re-design of the foundations, the raising of the central tower to reduce rock excavation at Beamer Rock, the complete re-design of the structural steel superstructure, the substitution of embankment for structures in the approach road networks and the global sourcing and procurement of materials for the project.
- Posted In:
- News
- Press Releases